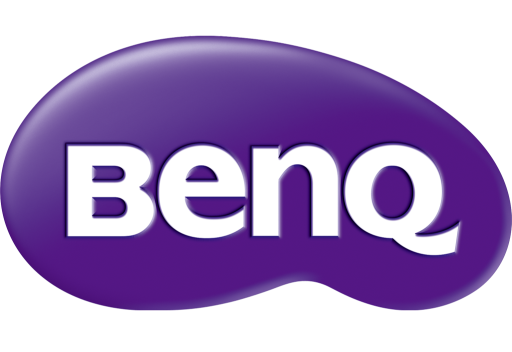
Projector
Explore All Projector Series
By Feature
Casual Gaming Best 4K Projectors Best Gaming Projectors Best Projectors for Sports: TV or Projector for Game Day Ceiling Projectors Outdoor ProjectorsBy Trending Word
4K UHD (3840×2160) Short Throw 2D, Vertical/Horizontal Keystone LED Laser With Android TV With Low Input LagExplore Commercial Projector
Professional Installation Simulation Projection Small Business Corporation K12 & Higher Education Golf Simulator Projector
Monitor
Explore All Monitor Series
By Feature
Photographer Monitors Designer Monitor Best 4K Monitors Best Monitors for MacBook Pro & Mac 2025 Best Monitors for Versatile MacBook Users Best Monitor for Programming
Lighting
Remote Work & Learning
Explore treVolo Speaker
Dialogue Speaker for Learning Electrostatic Bluetooth Speaker Carry Case & Stand